What is faceting|The difference between Edo faceting, Satsuma faceting, and Otaru faceting and its charm
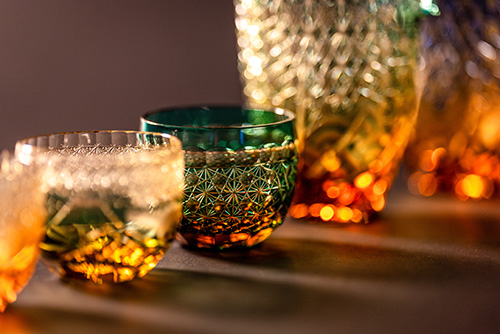
Faceting is one of Japan's traditional glass craft techniques. A rotating metal wheel is pressed against the surface of the glass with an abrasive to create a unique design by grooving and polishing. Products made with this technique are also called faceted. The name "faceted glass" is said to derive from "kiriko-gata," which refers to the shape of a cube with its corners cut off.
This article describes the faceting we carry in our showroom, "type of faceted glass from Edo", "Satsuma cut glass (type of faceted glass)", "Otaru faceted glassWe will focus on three of the three and discuss the differences and attractions of each.
Article
History of faceting
Before describing each facet, we will discuss the history of faceting.How was the faceting technique introduced?Cut glass was brought to Japan by missionaries during the Age of Exploration in the 16th century.This was the beginning. Later, glass production began in Nagasaki, and in the Edo period (1603-1867), glass was produced in Osaka, Edo, Satsuma, and other parts of Japan.
Japanese faceting developed independently based on Western techniques. There are differences in raw materials and manufacturing methods. In Japan, lead glass was used, and the technique of creating cut patterns by manual friction continued until the early Meiji period.
type of faceted glass from Edo
Edo Kiriko is,Faceting technique born in Edo town in the late Edo period.It is. Edo faceting, which developed from the culture of the common people, is characterized by its delicate and beautiful carving techniques.
> >Click here for sales website
feature
Glass Structure
Edo faceting is a double-layered structure of thinly colored glass blown into a glass mold and then overlaid with a layer of clear glass.The following is a list of the most common problems with the
Cutting Features
Edo faceting is characterized by clear, thin cut lines. The contrast between the transparent glass and colored glass is sharp and clear.The following is a list of the most common problems with the
color
Although today's Edo faceting is characterized by a wide variety of colors, when it was first made in the Edo period, it was mostly colorless and transparent.
sense of touch
The cut is deeply dug in for an edgy, tactile feel.
design
Edo faceting has a variety of patterns, each with its own meaning. Typical patterns include the igoko motif, kikutsugi motif, hexagonal kagome motif, octagonal kagome motif, chrysanthemum motif, hemp leaf motif, bamboo leaf motif, arrowhead motif, cloisonne motif, and tortoiseshell motif. These patterns are,Auspiciousness and traditional significanceand are popular as gifts.
Satsuma cut glass (type of faceted glass)
Satsuma faceting was born in the Satsuma domain (present-day Kagoshima Prefecture) at the end of the Edo period. Unlike Edo faceting, it initially developed as a business under the direct control of the clan.
> >Click here for sales website
feature
Glass Structure
Satsuma faceting uses a unique process of layering two layers of clear glass and colored glass.1. This increases the overall thickness of the product, giving it a sense of weight when held in the hand.
Cutting Features
The most distinctive feature of Satsuma faceted glass is a unique gradation called "Bokashiis. The boundary between the cut and the color is blurred, giving the overall impression of blurriness.
color
Satsuma faceted glass is made by covering transparent glass with colored glass. By cutting, colored areas and transparent areas are created, creating an exquisite gradation.
sense of touch
Satsuma faceting is made by increasing the thickness of the glassGory to the touch and massive to the touchand has a unique comfort.
design
Satsuma faceting also has its own unique patterns. Typical examples are the ring knot pattern, Satsuma stripes, fish pattern, stepped sword and chrysanthemum pattern, hobnail, octagonal baskets, hemp leaf pattern, chrysanthemum flower pattern, and tortoise shell pattern. Many of these patterns are designed using the "bokashi" technique, which is a characteristic of Satsuma faceted glass, and create a beauty with depth.
Otaru faceted glass
Otaru faceting is a faceting technique born in Otaru City, Hokkaido. Although it has a shorter history than Edo faceting or Satsuma faceting, it has its own unique charm.
> >Click here for sales website
feature
History
Otaru facets are,Glass industry started in Otaru in the Meiji EraThe company developed from It was born out of the demand for durable glass products suited to Hokkaido's harsh climate.
design
The designs are characterized by Hokkaido's natural motifs. Many of the cut patterns are inspired by snow crystals and drift ice.
color
Otaru faceting is characterized by cool blue and green tones. This is inspired by the sea and forests of Hokkaido.
technique
Otaru faceting has developed in its own unique way while incorporating Edo faceting and Satsuma faceting techniques. It is characterized by the use of thick glass and deep, powerful cuts.
Faceting manufacturing process
1. allocation
Allotment is the first step in the faceting process, in which markers are drawn on the glass surface in accordance with the design. This is an important preparation for a precise finish, and the overall balance and shape of the piece is determined at this stage.
2. coarse grinding
In the roughening process, the glass is roughened along the markers indicated in the allocation process. This is the main process of shaping the glass, and a rough design is formed using specialized tools. This is an important process that forms the basis for the finishing work that follows.
3. stone hanging
Ishikake is the process of further sharpening the surface that has been roughly prepared by rough grinding to make the design clearer. Fine grinding stones and tools are used to smooth the surface and accentuate the precise pattern.
4. polishing
Polishing is the final finishing process to bring luster to the glass surface after it has been stoned. Polishing is done using abrasives and special machinery,Transparency and beautiful shineThe process gives the faceted surface its unique and gorgeous reflections of light. This process produces the gorgeous reflections unique to faceting.
Although there are differences in the detailed techniques and finishes between Edo faceting, Satsuma faceting, and Otaru faceting, the basic manufacturing process can be summarized in these four steps.
Edo faceted glass, Satsuma faceted glass, Otaru faceted glass, which you can feel in Sapporo
At "Japanese Modern N6 Kita Maruyama" in Kita Maruyama, Sapporo, the beauty of Edo faceted glass, Satsuma faceted glass and Otaru faceted glass isYou can actually see and feel the product in your hands.The faceted glass is famous for its traditional craftsmanship. Faceting is a renowned traditional craft, but the differences in texture and cut of each piece cannot be fully conveyed through photos and videos. This space allows visitors to directly compare facets from all over Japan while in Sapporo.
Only in a showroom can you experience the sparkling transparency of faceted glass through the light, the delicate cut to the touch, and the beauty of the craftsmanship up close. At WA-MODERN N6 Kita Maruyama, you can enjoy the individuality of each faceted piece while actually holding it in your hand.
We hope you will enjoy the charm of traditional Japanese crafts in Sapporo.
summary
Faceting is one of the most fascinating techniques in Japanese glass art. Edo faceting, Satsuma faceting, and Otaru faceting each have their own unique history and characteristics, reflecting the culture and techniques of each region of Japan. These facets are not merely beautiful crafts, but are valuable embodiments of Japanese culture and history.